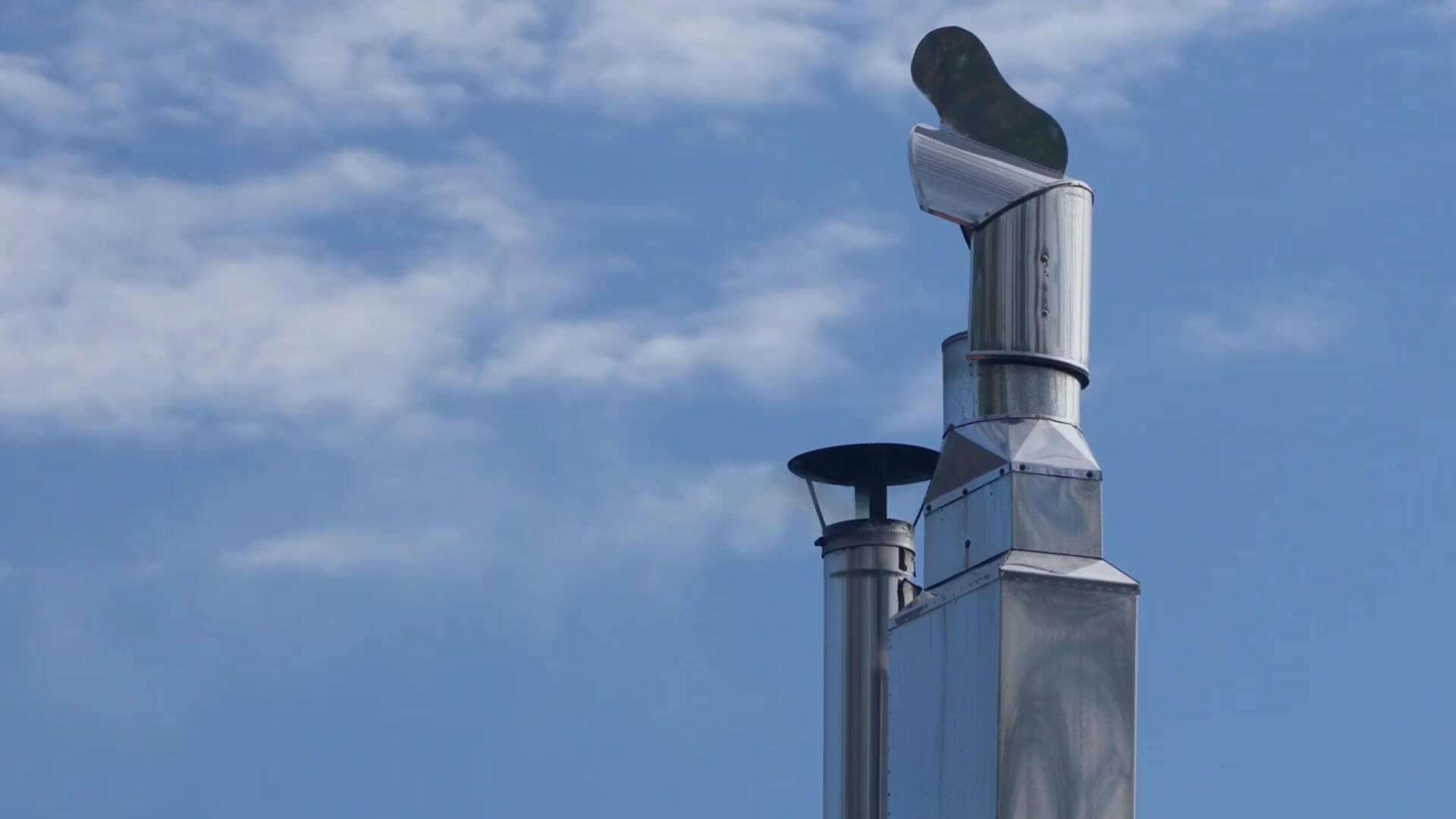
Drupps Vapor Case Study
What an actual Drupps Vapor case looks like in terms of numbers
Drupps Vapor Case Study
Summary
In this study, Drupps Vapor was installed at a ceramic tile factory.
It recovered 5,000—6,000* kg/h of water from a system with a maximum water evaporation of 9,000 kg/h.
The system recovered around 400 kWt of heat from a 193 kWe dryer.
Return on investment for this case was less than 5 years.
*Depending on fan control mode
Drupps Vapor Case Study
A simplified description of the process
Drupps Vapor connects to the outlet airflow of the dryer via an air duct.
Recovered heat is fed back to the inlet side of the dryer as hot water.
Drupps Vapor Case Study
Physical Appearance
The size of the airflow coming from the dryer required two Vapor modules to be included in this system.
The dry cooler’s capacity and size was adapted to local climate conditions.
Drupps Vapor system was placed outdoors in direct connection to the building housing the dryer.
Drupps Vapor Case Study
Results
Fan Control Modes
Performance — Optimized for water production
Balanced — Optimized for total savings
Efficient — Optimized for running cost (electricity)
Drupps Vapor Case Study
Results
Water and heat recovery varies over the year and moves in tandem with changing climate conditions.
Warmer weather affects production capacity negatively.
Drupps Vapor Case Study
Climate Data
These were the local climate conditions for this site. Yearly temperature average is 16°C.
Ambient air conditions affects the cooling conditions of the Drupps Vapor system.
Do you want to know more?
To download technical specification please contact us